Battery
Redefining speed and precision in battery inspection
Battery defects are often microscopic, hidden deep within the cell structure, and impossible to detect from the outside. Conventional 2D X-ray and sample-based testing miss critical internal flaws, while slower computed tomography (CT) systems create production bottlenecks. But with Excillum’s MetalJet X-ray technology, manufacturers can achieve high-speed inline CT with the resolution, power, and speed needed to inspect every cell — without slowing down production.
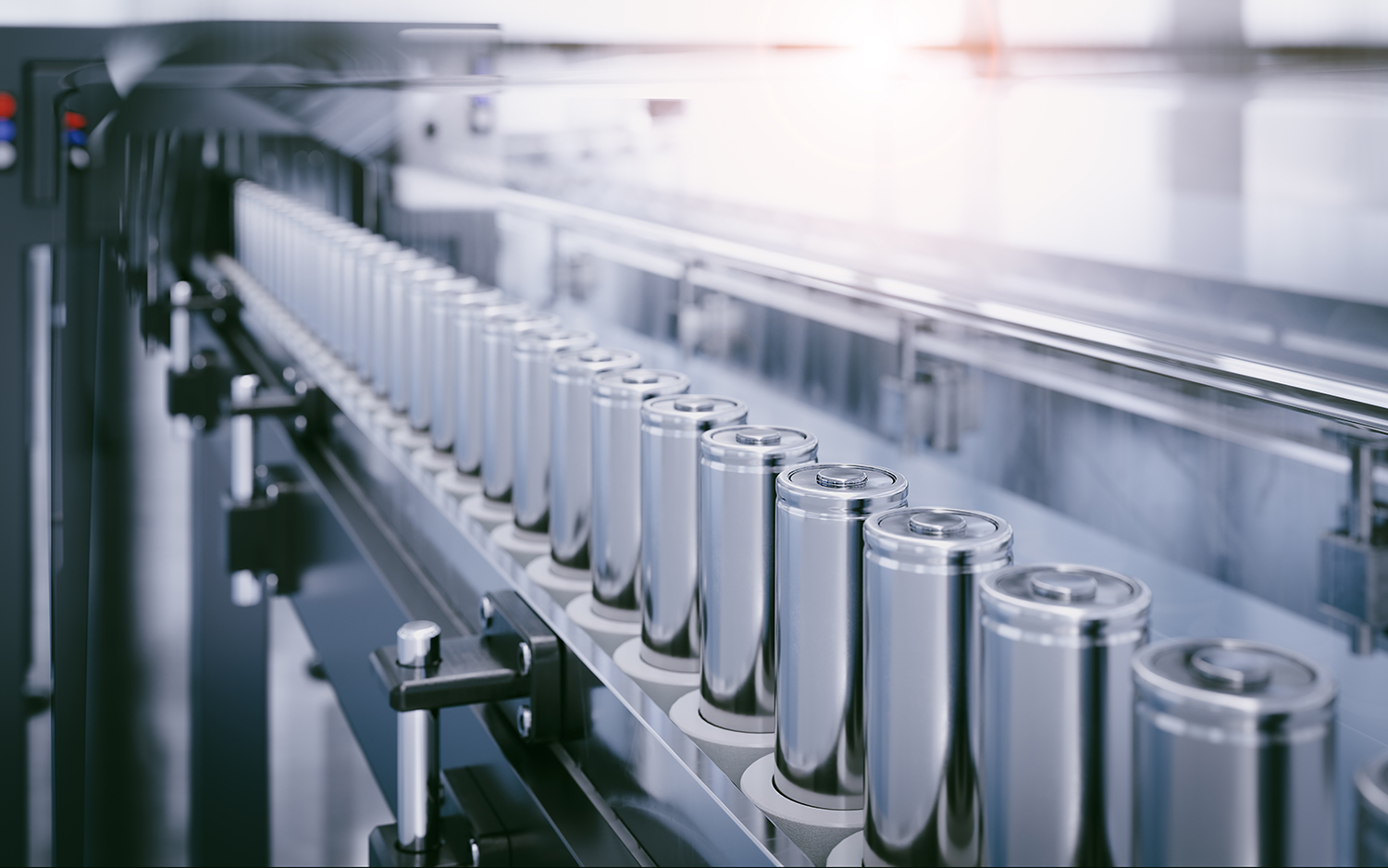

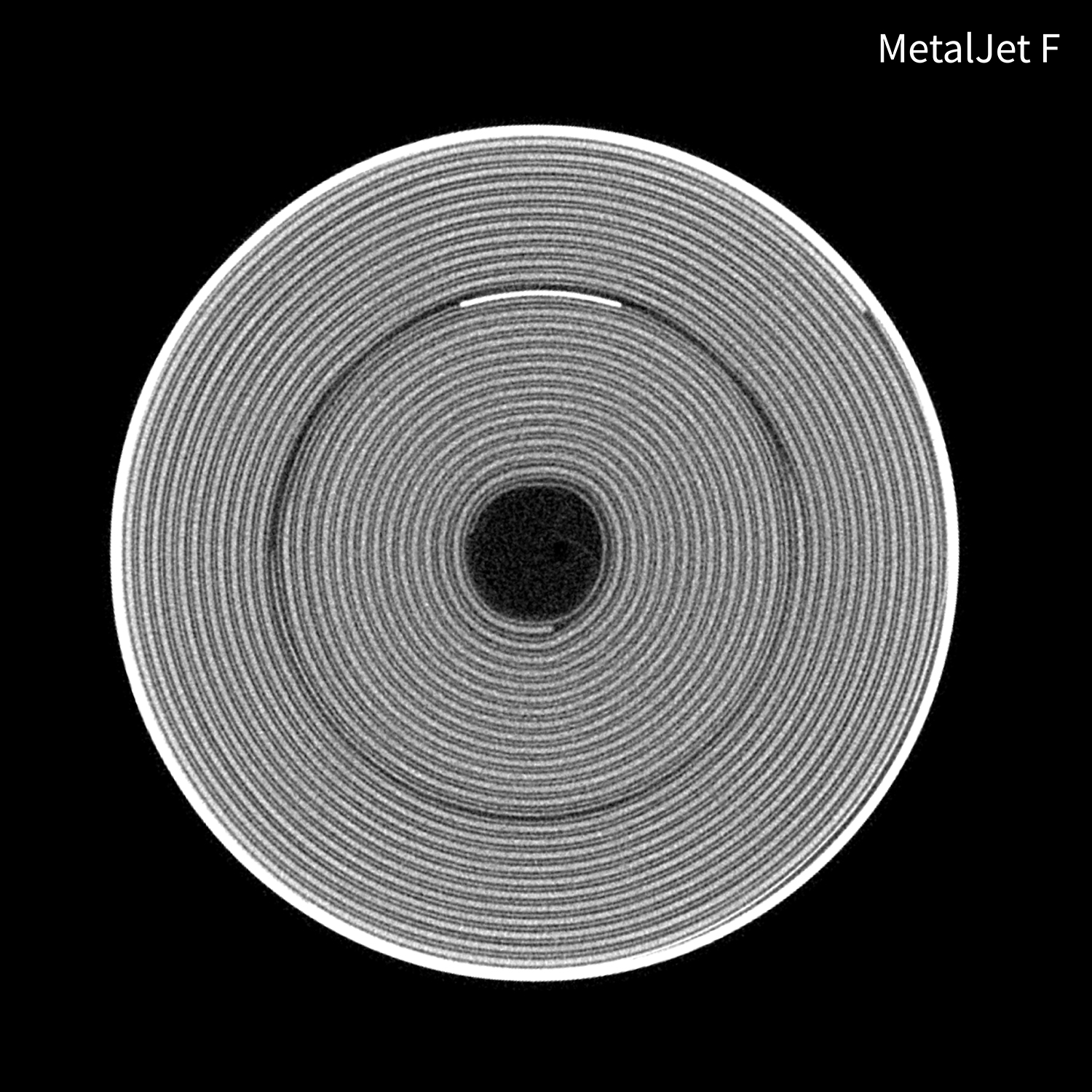
2170 cell scanned with a conventional vs a MetalJet F microfocus X-ray source
Excillum X-ray sources push the limits of today’s most advanced CT techniques, delivering sharper images, faster scans, and the ability to detect defects smaller than ever before. The result? A new standard in battery inspection — ensuring safer, higher-quality, and more efficient battery production.
Typical defects for 3D X-ray inspection
- Electrode misalignments (AC overhang)
- Internal voids
- Foreign particles contamination
- Jellyroll buckling
- Delamination
- Welding defects
- Cracks in electrodes or casing
Application examples
Cylindrical battery cells are the backbone of electric vehicle (EV) energy storage, offering a balance of energy density, reliability, and manufacturability. Over the years, these cells have evolved from the widely used 18650 and 2170 formats to the latest generation 46xx, which features a larger form factor and advanced design for improved performance.
However, ensuring quality in cylindrical cell manufacturing is critical, as defects such as electrode misalignments, internal voids, and contamination can lead to reduced efficiency, increased scrap rates, or even safety risks. High-speed, high-resolution inspection solutions are essential for detecting these issues early — optimizing production yield and ensuring the safety and performance of every cell.
With the MetalJet F, region of interest (ROI) scans can be done in less than 1 second, and full cell scanning can be achieved in the matter of a few seconds.
Pouch battery cells are a flexible and lightweight energy storage solution, widely used in both electric vehicles (EVs) and consumer electronics. Their thin, laminated design allows for higher energy density and efficient space utilization, making them ideal for applications where weight and form factor are critical.
In EVs, pouch cells enable custom battery pack designs with improved cooling and packaging efficiency. In consumer electronics, they provide compact, high-performance power for smartphones, laptops, and other portable devices. However, their flexible casing makes them more susceptible to defects such as swelling, delamination, and internal contamination — issues that can compromise performance, lifespan, and safety. Advanced inspection techniques are essential for detecting these defects early, ensuring reliability, and maintaining the highest quality standards in mass production.
With the MetalJef F either region of interest (ROI) scans, or full cell scans can be done – depending on form factor of the cells.
Prismatic battery cells offer a structured and space-efficient energy storage solution, widely used in electric vehicles (EVs) and energy storage systems. Their rigid aluminum or steel casing provides mechanical stability and improved thermal management, allowing for higher capacity and longer cycle life compared to other formats.
However, manufacturing challenges such as welding defects, electrolyte leaks, and internal misalignments can impact performance and safety. High-precision inspection solutions are essential to detect these issues early, ensuring consistent quality, reliability, and safety in large-scale battery production.
With the MetalJet F region of interest scans of the corner of prismatic cells can be achieved in 1 second or less – to study e.g. electrode alignment.
Pushing the boundaries of battery performance starts with a deeper understanding of materials at the micro and nano level. As battery designs evolve and new chemistries emerge, researchers need tools that deliver unmatched insights into the internal structure of cells and materials.
Excillum’s X-ray sources, with their unique combination of high flux and/or small spot size, empower researchers to visualize and analyze battery materials in unprecedented detail. Whether it’s studying electrode microstructures, particle distributions, or identifying material defects, Excillum enables advanced nano- and micro-CT imaging to accelerate discoveries and optimize next-generation battery technologies.
Battery microstructures
The video below shows a NanoCT of a lithium ion battery cathode material, where the microsctructure of the material can be clearly resolved. Both the aluminum cathode collector and the active LiCoO2 layer are visualized and can be analyzed further thanks to the high resolution enabled by the small X-ray spot of the Excillum NanoTube N3.
These results were generated at the applications lab at Excillum in Sweden, using our NanoTube N3 and a detector from Dectris. Visualization and analysis was made using ORS Dragonfly.
Battery particle sizes
In the image below, a 3D rendering of the NanoCT of a lithium ion battery cathode (NCA/LCO-E) shows particles of different sizes. Voxel sampling 140 nm.
This NanoCT system with the Excillum NanoTube has been designed, developed and commissioned at Fraunhofer IIS, Würzburg, Germany. Together with an EIGER2 CdTe detector, the system has been optimized for materials characterization and NDT applications.
Interested in a demonstration?
Together with our partners, we have demonstrators where you can experience first-hand the capabilities of our high-speed 3D CT inline inspection system.
Are you interested in advanced battery quality evaluation? Fill out the form below to book a demo with us!
Powered by partnerships
Excillum’s sources are an integral part of system development for some of the most trusted names in X-ray instrumentation. Together, we work intensely to put the benefits of MetalJet and NanoTube sources into the hands of users everywhere.